

Vertical, lateral, oenological agitators, vertical emusifier, bottom or inline emulsifiers, and micronisers … If you take a few minutes to look closely at all the pages on our website, you will see that we have an extensive range of machines, which allow us to cover most of the current applications within the food, cosmetic, pharmaceutical and chemical sectors. This information is intended as a guide and does not relieve the user of completely analyzing the entire mounting system.Blender mixers are not the only type of agitator machinery that we manufacture and market. Refer to Table 2, page 4 for mounting dimensions. See Figure 1, page 2 (GTD) or Figure 2, page 3 (GTP). Beams of equivalent section modulus and moment of inertia and/or modulus of elasticity can be used. Select the appropriate beam size for you application. Table 3, page 4, Recommended Beam Sizes is keyed to model, a case size and tank diameter.

Refer to the agitator assembly drawing for the support structure design loads. The structure should be sufficiently rigid that the agitator extension shaft will not move more than 1/32 inch per foot (2.6 mm per meter) of length due to deflection of the structure. The support structure must be rigid enough to support the agitator weight and the live agitator reactions as a result of torque and bending moment. The agitator has been designed to accommodate these forces, and as a result, the forces are transmitted directly to the mounting support. The net effect of the turbine thrust force is to offset or add to the unit weight, contributing to the variability of the support structure loading. Upward pumping turbine thrust force will add to the unit weight.
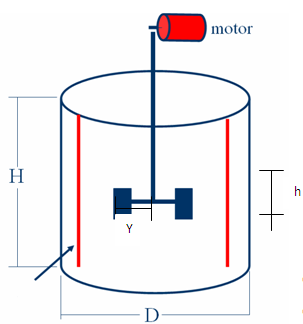
The thrust force is generally less than the weight of the unit. A pitched blade or axial flow turbine normally pumps downward and generates an upward thrust. Because of the random nature of the forces and the rotation of the shaft, the direction of these forces is constantly changing.
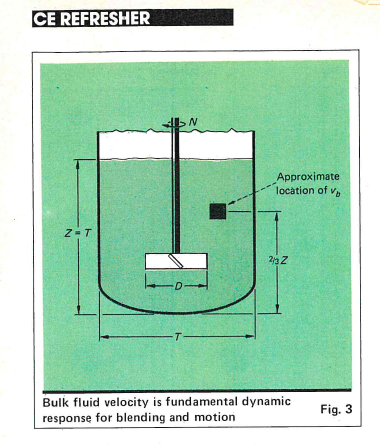
Hydraulic forces acting on the turbine generate moments, which act on the shaft and are transmitted to the agitator drive. Start up of the agitator with the turbine impacted in solids is beyond the scope of these recommendations.
AGITATOR DESIGN PLUS
Torque implies an unchanging load, but the actual operating torque will show plus or minus 10 to 20 percent variability due to the turbulent conditions within the agitated fluid. The forces and moments produced by the turbine rotating in a fluid are torque, turbine thrust and turbine hydraulic (side) force. During operation of the agitator, the fluid motion in the vessel produced by the rotation of the turbine impeller can exert significant forces and moments on the agitator extension shaft. Do not mount on a surface which is not flat and horizontal. The agitator extension shaft is designed to run in a true vertical position. The most frequent cause of mechanical difficulty with an agitator is improper mounting. Refer to the agitator assembly drawing for minimum required mounting height to allow for servicing the seal. GTD style units may include an auxiliary shaft seal as an option. GTD/GTP Turbine Agitators Mounting SupplementĪGITATOR MOUNTING GTD and GTP (open tank) style units usually mount separately from the tank on either a steel structure or a concrete slab over the tank.
